yard shed kits costco
Thursday, November 21, 2024
Free Pallet Shed Plans: Build a Practical Storage Solution for Your Yard
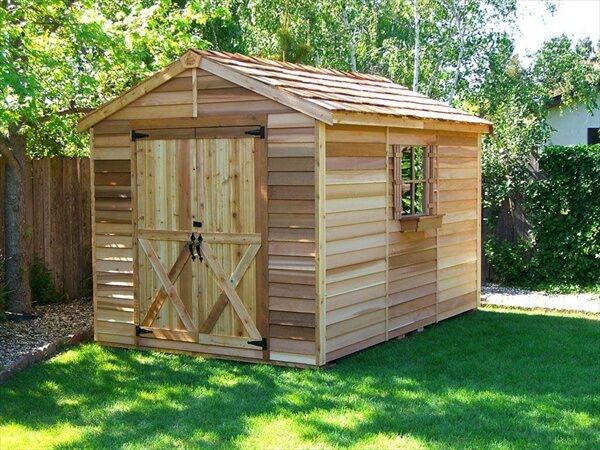
Free Pallet Shed Plans: Build a Practical Storage Solution for Your Yard
Tired of clutter overflowing your garage and yard? Yearning for a stylish yet functional storage solution that doesn't break the bank? Look no further! This guide provides free pallet shed plans that transform readily available pallets into a practical and surprisingly attractive addition to your outdoor space. We'll walk you through every step, from gathering materials to the final touches, ensuring you build a sturdy and weather-resistant shed that perfectly complements your property.
Gathering Your Materials: The Foundation of Your Pallet Shed
Before you even think about hammering a nail, you need to source your materials. The star of the show, of course, is the reclaimed pallet. Free pallets are often available from businesses like grocery stores, construction sites, or even on online classifieds. Inspect them carefully; choose sturdy pallets with minimal damage. Avoid pallets showing signs of pest infestation or chemical treatments. Beyond the pallets, you'll need additional materials, ensuring you have a robust structure. This includes:
- Strong screws: Opt for exterior-grade screws to withstand the elements.
- Wood glue: Enhances the structural integrity of your shed.
- Plywood or OSB sheeting (optional): For added weather protection and a more polished look.
- Roofing material: Consider asphalt shingles, metal roofing, or even sturdy tarpaulin for a cost-effective option.
- Measuring tape, level, saw, drill, and safety glasses: Essential tools for a safe and efficient building process.
Remember to assess your existing yard space to determine the optimal size and location for your pallet shed. Consider proximity to power outlets or water sources if you plan on utilizing the shed for specific purposes.
Constructing the Frame: Building a Solid Base
Laying the Foundation
Begin by constructing the base frame of your pallet shed. This provides the essential support for the entire structure. You can create a simple rectangular frame using four sturdy pallets laid on their sides and secured together using screws and wood glue. Ensure the frame is level and stable. For additional strength, consider adding a concrete foundation or a level layer of gravel beneath your pallet base. This will prevent the shed from sinking into soft ground.
Erecting the Walls
Next, assemble the walls of your shed using additional pallets. You can stand the pallets vertically and secure them to the base frame using screws and wood glue. Remember to carefully align the pallets to create straight and even walls. For increased stability, consider reinforcing the corners with additional wooden supports or bracing.
Completing the Roof
Construct the roof frame using additional pallets or lumber, creating a gable or shed roof design depending on your preference. Attach the roofing material securely to the frame, ensuring it's waterproof and durable. Consider adding a small overhang to protect the walls from rain. Remember that proper roof construction is vital for protecting your shed's contents from the elements.
Adding Finishing Touches: Personalizing Your Pallet Shed
Once the basic structure is complete, you can personalize your shed with various finishing touches. Consider adding a simple door constructed from additional pallets or plywood. You could also add windows for ventilation and light, enhancing both the aesthetic appeal and functionality of your storage space. A fresh coat of exterior paint or stain not only protects the wood but adds a pop of color to your outdoor space, blending seamlessly with your existing landscape. Remember to secure any exposed nails or screws to prevent injuries. Add a lock to secure your belongings.
Building your own pallet shed is a rewarding project that combines creativity with practicality. By following these free pallet shed plans, you can transform readily available materials into a functional and attractive storage solution, enhancing both the organization and aesthetics of your yard. So get started today and enjoy your newfound storage space!
Create a DIY Pallet Shed in Your Backyard: Easy-to-Follow Plans
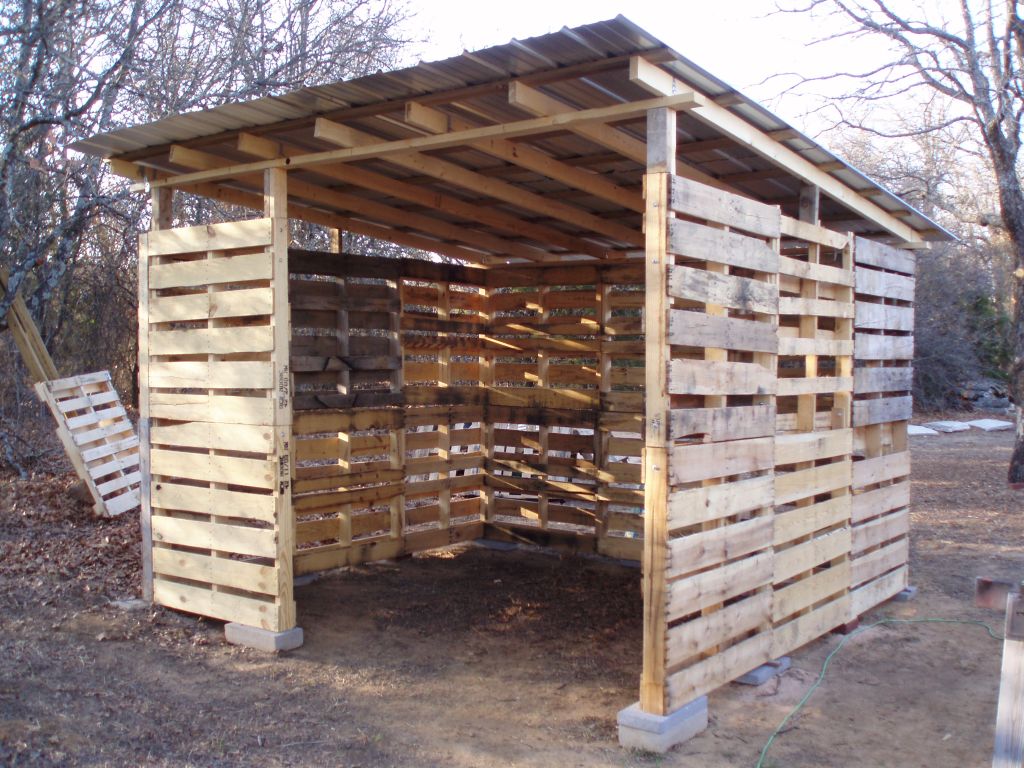
Constructing a DIY Pallet Shed in Your Backyard: A Comprehensive Guide
This guide provides a detailed, step-by-step plan for constructing a durable and aesthetically pleasing shed using reclaimed pallets. While seemingly a simple project, careful planning and execution are crucial for a structurally sound and long-lasting outcome. This guide prioritizes safety and provides comprehensive instructions to ensure a successful build.
Phase 1: Planning and Preparation
Before commencing construction, thorough planning is essential. This phase involves several critical steps that will significantly impact the project's success.
1.1 Site Selection and Permitting
Begin by carefully selecting the shed's location in your backyard. Consider factors such as proximity to utilities, access for construction and future maintenance, sunlight exposure (for natural ventilation and light), and aesthetic integration with the existing landscape. Check local building codes and regulations to determine if a permit is required for the construction of your shed. Obtain any necessary permits before beginning construction to avoid legal complications.
1.2 Pallet Acquisition and Assessment
Sourcing suitable pallets is a key aspect of this project. Avoid pallets treated with chemical preservatives (e.g., methyl bromide), as these can pose health risks. Look for heat-treated pallets, which are marked with an HT stamp. Inspect each pallet carefully for rot, damage, or loose boards. Aim for pallets of consistent dimensions and structural integrity. The number of pallets required will depend on the desired shed size. It's advisable to acquire more than initially estimated to account for potential damage or unusable sections.
1.3 Design and Dimensions
Create a detailed design plan, including detailed dimensions for the shedâs length, width, and height. Consider the intended use of the shed to determine the necessary interior space. Drawings and diagrams are highly recommended to visualize the structure and ensure accurate material estimations. Consider incorporating features such as a door, windows (for ventilation and light), and a roof overhang. Simple designs are generally easier to construct for novice builders.
1.4 Material Gathering
Beyond the pallets, you will need additional materials. This includes:
- Foundation materials: Concrete blocks, gravel, or a level concrete slab.
- Fasteners: Galvanized screws of various lengths for joining pallets and other components.
- Roofing material: Tarpaulin, corrugated metal sheets, or asphalt shingles.
- Door hardware: Hinges, latch, and handle.
- Window frames and glazing (optional): Choose weather-resistant materials.
- Wood sealant or paint (optional): To protect the wood and enhance the shedâs appearance.
- Safety equipment: Gloves, safety glasses, and a work mask.
Phase 2: Foundation and Base Construction
A stable foundation is critical for the longevity and structural integrity of the shed. This section details the construction of a suitable base.
2.1 Leveling the Ground
Begin by clearing the designated area of any vegetation, debris, or uneven ground. Use a level to ensure the ground is completely level. If necessary, adjust the ground level by adding or removing soil. A properly leveled base is essential for a square and stable structure.
2.2 Foundation Construction
Several foundation options exist, each with its own advantages and disadvantages. A simple and effective option is to use concrete blocks arranged to create a level base. Alternatively, you could use a gravel base for drainage, or pour a concrete slab for maximum stability. The chosen foundation should be level and capable of supporting the weight of the shed and its contents.
2.3 Pallet Base Frame
Once the foundation is in place, construct a frame using the most sturdy pallets. Secure these base pallets together using galvanized screws. Ensure the frame is square and level, using a measuring tape and level for accuracy. This frame will form the base of your shed and provide a solid foundation for the walls.
Phase 3: Wall and Roof Construction
This section outlines the construction of the shedâs walls and roof. Precision and attention to detail are vital at this stage.
3.1 Wall Assembly
Carefully assemble the pallet walls, ensuring that the pallets are tightly fitted and secured with screws. Use additional bracing, such as strategically placed wood supports, to enhance structural integrity, especially at corners. Vertical alignment is crucial to maintain a plumb and stable structure. Consider adding additional supports between the pallets to increase rigidity. The method for connecting the walls to the base frame should ensure stability and prevent racking.
3.2 Door and Window Installation (Optional)
If incorporating a door and windows, carefully cut openings in the pallet walls according to your design plan. Install pre-fabricated door and window frames or construct your own using appropriately sized lumber. Secure the frames firmly to the surrounding pallet walls.
3.3 Roof Construction
The roof design should complement the overall structure. A simple gable roof is a common and relatively easy-to-construct option. Construct the roof frame using additional lumber or repurposed pallet components. Ensure the roof frame is securely attached to the walls. Cover the roof with your chosen roofing material (tarpaulin, corrugated metal, or asphalt shingles), ensuring it's weatherproof and securely fastened.
Phase 4: Finishing Touches and Considerations
Once the main structure is complete, focus on the finishing touches and essential considerations.
4.1 Weatherproofing and Sealing
Apply a wood sealant or weatherproof paint to protect the pallets from moisture and the elements. This step will significantly extend the lifespan of the shed. Ensure complete coverage, paying close attention to all joints and exposed edges.
4.2 Final Inspection and Adjustments
Conduct a thorough inspection of the entire structure to ensure all joints are secure and the shed is stable and level. Make any necessary adjustments or repairs before proceeding.
4.3 Safety Precautions
Throughout the construction process, prioritize safety. Always wear appropriate safety gear, including gloves, safety glasses, and a work mask, especially when using power tools. Ensure the work area is well-lit and free of obstacles. If working at heights, use proper scaffolding or ladders and follow all safety guidelines.
Constructing a DIY pallet shed requires careful planning, attention to detail, and a commitment to safety. By following this comprehensive guide, you can create a functional and attractive addition to your backyard. Remember that adapting these plans to your specific needs and resources is key to a successful and personalized project.
Wednesday, November 20, 2024
Step-by-Step Lean-To Shed Build: How to Make a Reliable Shed

Step-by-Step Lean-To Shed Build: How to Make a Reliable Shed
Constructing a lean-to shed offers a practical and cost-effective solution for expanding storage or creating sheltered workspace. This guide provides a comprehensive, step-by-step approach to building a reliable and durable lean-to shed, emphasizing key considerations for material selection, structural integrity, and long-term performance.
Phase 1: Planning and Preparation
The foundation of any successful building project lies in meticulous planning. Before initiating construction, several critical steps must be undertaken to ensure a smooth and efficient process.
1.1 Site Selection and Assessment
Careful selection of the shed's location is paramount. Consider factors such as proximity to existing structures, access for delivery of materials, adequate sunlight (if needed), and drainage. Assess the ground's stability and levelness. Uneven ground requires leveling before foundation construction. Check local building codes and regulations regarding setbacks, height restrictions, and permit requirements.
1.2 Design and Dimensioning
Determine the desired dimensions of your lean-to shed based on your storage needs and available space. Sketch a detailed plan, including the dimensions of the base, walls, roof, and door. Consider the materials you will use and their dimensions when creating your design. A simple lean-to design is typically rectangular, with one side attached to an existing structure.
1.3 Material Selection
Selecting appropriate materials is crucial for the shed's durability and longevity. Consider the following:
- Foundation: Concrete slabs, gravel bases, or pressure-treated lumber are common choices. The choice depends on the soil conditions and the shed's weight.
- Framing: Pressure-treated lumber is recommended for its resistance to rot and decay. Choose dimension lumber appropriate for the shed's size and anticipated load.
- Sheathing: Plywood or OSB (oriented strand board) provides a strong and stable base for the roofing and siding.
- Roofing: Asphalt shingles, metal roofing, or polycarbonate sheets are suitable options. Consider the climate and your budget when making your selection.
- Siding: Various materials are available, including wood, vinyl, and metal. Choose a material that matches the aesthetic of your existing structures and offers adequate protection from the elements.
- Hardware: Use galvanized or stainless steel screws, nails, and other fasteners to resist corrosion.
1.4 Acquiring Necessary Tools and Equipment
Gather all necessary tools and equipment before beginning construction. This might include:
- Measuring tape
- Level
- Shovel
- Post-hole digger (if needed)
- Circular saw
- Drill with various drill bits
- Hammer
- Safety glasses
- Work gloves
- Safety boots
Phase 2: Foundation and Framing
With planning complete, the construction phase begins. A solid foundation ensures the shed's stability and longevity.
2.1 Foundation Construction
Prepare the ground by leveling the area and removing any vegetation. For a concrete slab foundation, pour a level concrete slab of appropriate thickness, ensuring proper curing time before proceeding. Alternatively, a gravel base provides a simpler, more cost-effective option, providing drainage and a level surface. For a less permanent option, pressure-treated lumber can be used to create a raised foundation.
2.2 Framing the Base
Construct the base frame using pressure-treated lumber. This frame will support the walls and roof. Ensure squareness and accurate measurements throughout this process. Use appropriate fasteners to securely join the lumber.
2.3 Wall Framing
Erect the wall frames, ensuring they are plumb and properly aligned with the base frame. Use appropriate bracing to maintain structural integrity during construction. For a lean-to, one wall will be attached to the existing structure. Ensure proper fastening to the host structure.
2.4 Roof Framing
The roof framing involves constructing rafters that slope from the higher point of the existing structure to the lower edge of the lean-to. Calculate the rafter lengths and angles accurately to ensure proper roof pitch and drainage. Securely attach the rafters to both the existing structure and the lean-to frame.
Phase 3: Sheathing, Roofing, and Siding
Once the framing is complete, the shed's exterior is enclosed and weatherproofed.
3.1 Sheathing the Walls and Roof
Attach plywood or OSB sheathing to the wall and roof frames, ensuring proper alignment and fastening. This provides a solid surface for the roofing and siding materials.
3.2 Roofing Installation
Install the chosen roofing material according to the manufacturer's instructions. Ensure proper overlapping and sealing to prevent leaks. Pay close attention to flashing around the edges and any penetrations (e.g., vents).
3.3 Siding Installation
Install the siding material, ensuring proper overlapping and sealing to protect the shed from the elements. Maintain a consistent gap for ventilation. Consider adding trim pieces for a finished look.
Phase 4: Finishing Touches and Inspections
The final phase involves completing the door, windows (if applicable), and conducting a thorough inspection.
4.1 Door Installation
Install the shed door, ensuring proper alignment and secure fastening. Consider adding weatherstripping for added protection from drafts.
4.2 Final Inspections
Conduct a thorough inspection of the entire structure, checking for any loose fasteners, gaps, or other issues. Address any imperfections before considering the shed complete.
4.3 Finishing Considerations
Consider adding features such as painting, staining, or sealing the exterior to enhance the aesthetic appeal and protect the materials. You might also want to install shelving or other interior features based on your storage requirements.
Building a lean-to shed requires careful planning, attention to detail, and a commitment to safety. By following these steps, you can construct a reliable and durable shed that will serve its purpose for years to come. Remember to always prioritize safety and consult with professionals if needed.
Saturday, November 16, 2024
Customize Your 12x20 Shed with Loft Plans

Customizing Your 12x20 Shed with Loft Plans: A Comprehensive Guide
The humble shed, once relegated to the back corner of the property for storing garden tools and forgotten lawnmowers, is experiencing a renaissance. Modern shed designs now offer versatile spaces for a multitude of uses, from workshops and home offices to guest accommodations and even creative studios. The addition of a loft significantly expands the potential of a 12x20 shed, doubling the usable space and unlocking a range of exciting possibilities. This guide will explore the process of customizing a 12x20 shed with loft plans, offering insights into design considerations, construction techniques, and regulatory compliance.
Phase 1: Conceptualization and Planning
Before a single nail is hammered, careful planning is crucial. This phase involves defining the shed's purpose, determining the loft's function, and selecting appropriate materials. Thorough planning minimizes unforeseen complications and ensures a successful project.
Defining the Shed's Purpose
The intended use dictates many aspects of the design. A workshop requires ample workbench space and robust electrical systems, while a guest house prioritizes comfort and insulation. Consider the following:
- Primary function: Storage, workshop, home office, guest room, hobby space, etc.
- Secondary functions: Additional storage, workspace, relaxation area, etc.
- Frequency of use: Will the shed be used daily, weekly, or only occasionally?
Designing the Loft
The loft's design should complement the shed's primary function. Careful consideration of headroom, access, and structural integrity is essential. A low loft may suffice for storage, but a sleeping loft requires significantly more headroom. The access point â" a staircase or ladder â" is another critical design element. A staircase offers greater convenience but necessitates more floor space, while a ladder is more compact but less accessible.
- Loft function: Storage, sleeping area, home office, etc.
- Headroom: Minimum 6 feet for comfortable standing; consider taller for sleeping areas.
- Access: Staircase or ladder â" weigh convenience against space requirements.
- Structural support: Adequate framing and support beams for the loft floor.
Material Selection
The choice of materials impacts the shed's durability, aesthetics, and cost. Pressure-treated lumber is essential for longevity, particularly for the foundation and framing. Consider using durable siding materials like vinyl, metal, or composite for low-maintenance exterior finishes. For the loft floor, plywood or engineered wood is recommended for strength and stability. Insulation is crucial for temperature control, especially if the shed will be used year-round or as a guest house.
- Framing: Pressure-treated lumber for foundation and framing.
- Siding: Vinyl, metal, composite, or wood.
- Roofing: Asphalt shingles, metal roofing, or other weather-resistant materials.
- Flooring: Plywood, engineered wood, or other durable flooring materials.
- Insulation: Fiberglass, cellulose, or spray foam insulation for walls and ceilings.
Phase 2: Construction and Installation
This phase involves the actual construction of the shed, including the foundation, framing, exterior finishes, and the loft structure. Accurate measurements, proper assembly, and adherence to building codes are vital for a safe and structurally sound shed.
Foundation Construction
A solid foundation is the cornerstone of any successful shed project. Options include concrete slabs, pier and beam foundations, or even a gravel base, depending on the soil conditions and local building codes. Proper grading and drainage are essential to prevent water damage.
Framing and Exterior Finishes
The shed's framing provides the structural support for walls, roof, and the loft. Properly spaced studs and rafters ensure strength and stability. Once the framing is complete, the exterior finishes â" siding, roofing, and windows â" can be installed. Pay close attention to weather sealing to prevent leaks and drafts.
Loft Construction
The loft construction is a crucial step. Begin by installing support beams and joists to create a robust floor system. Ensure that the loft floor is securely attached to the main framing of the shed. The stairs or ladder access must be carefully planned and securely installed. Consider adding handrails for safety.
Electrical and Plumbing (if applicable)
If the shed will be used as a workshop, home office, or guest house, electrical wiring and potentially plumbing will be necessary. This requires professional expertise to ensure compliance with building codes and safety regulations. Consult with a qualified electrician and plumber for this aspect of the project.
Phase 3: Finishing and Compliance
The final phase involves interior finishing, ensuring compliance with local regulations, and obtaining any necessary permits.
Interior Finishing
Once the structure is complete, focus on the interior finishes. This includes installing drywall or paneling, flooring, painting, and any built-in features like shelving or cabinets. Consider adding insulation to enhance energy efficiency and comfort.
Building Codes and Permits
Before starting construction, check with your local building department to determine whether permits are required and what building codes apply. Failure to comply with regulations can result in fines or even demolition orders. Obtain all necessary permits before beginning construction.
Safety Considerations
Throughout the entire process, prioritize safety. Use appropriate personal protective equipment (PPE), such as safety glasses, gloves, and hearing protection. Follow all manufacturer's instructions for tools and materials. If you're unsure about any aspect of the construction, consult with a qualified professional.
Customizing a 12x20 shed with loft plans offers a rewarding experience, transforming a simple storage unit into a functional and versatile space. By meticulously planning each phase, selecting appropriate materials, adhering to building codes, and prioritizing safety, you can create a customized shed that perfectly meets your needs and enhances your property.
Monday, November 11, 2024
How to Design and Build a Pole Barn for Any Purpose
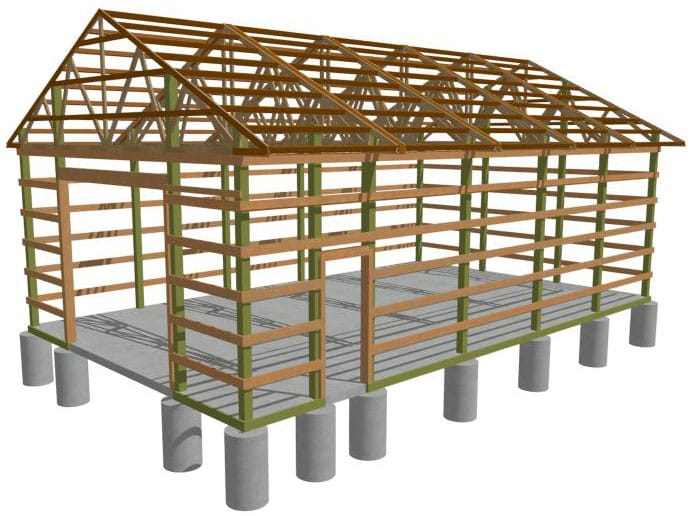
So, you're ready to take on a big project, huh? Building a pole barn is a fantastic way to add versatile space to your property, whether you need a workshop, a garage, a stable for your horses, or even a quirky living space. It's a surprisingly attainable DIY project, and I'm here to guide you through the whole process, from dreaming up the perfect design to seeing it come to life.
First Things First: Planning the Perfect Pole Barn
Before you start digging holes, you gotta have a solid plan. This includes figuring out the size, purpose, and design features that will make your pole barn perfect for you.
The Size Matters: Think about how you'll use the space and how much stuff you need to store. A small workshop might only need 12x20 feet, while a large barn for equipment could be 30x40 feet or even bigger. Don't forget to consider the layout you want, like separate areas for storage, workbenches, or even a living space.
Purpose is King: What's this barn for? Storage? A workshop? A place to park your shiny new car? Each purpose dictates different needs, like height for vehicles, ventilation for livestock, or insulation for a comfortable living area.
Design Details: This is where your creativity kicks in! Do you want a simple gable roof or something more fancy? Are you going for a rustic look with wood siding or a modern vibe with metal? Think about the overall style you want and what materials will work best.
Getting Your Hands Dirty: The Construction Process
Now, let's get down to the nitty-gritty. Building a pole barn is a journey, not a sprint, so we're going to break it down into manageable steps.
1. Site Preparation:
Get Those Permits: You'll need building permits, so check with your local authorities. They'll ensure your design meets local codes and regulations.
Leveling the Playing Field: Make sure your chosen spot is level, especially for a garage or workspace. You might need to grade the area or bring in fill dirt to get it right.
Foundation Footings: This is where the magic begins! Dig holes for concrete footings, which will support the poles. Make sure they're deep enough to reach solid ground and are spaced according to your plan.
2. The Poles Are Up!
Choosing Your Timber: Poles are typically made of pressure-treated lumber, like southern pine or cedar. They're sturdy and resistant to rot, making them ideal for this type of construction.
Erecting Those Giants: With the footings set, you'll lift and secure the poles, making sure they're plumb (perfectly vertical). You might need some help from a friend for this part, especially for taller poles.
Connecting the Dots: Once the poles are up, you'll connect them with beams, girders, and bracing. This creates the framework for your roof and walls.
3. Roofing and Siding:
Building the Roof: The roof is your shield against the elements, so choose wisely! Gable roofs are popular for their simplicity, but you can also go with hip roofs, gambrel roofs, or even flat roofs. Remember to install the roof sheathing and shingles to match your chosen style.
Walling It In: Now it's time to choose your siding. Wood siding offers a classic look, while metal siding is low-maintenance and durable. Whichever you choose, ensure it's securely attached to the framing.
4. Interior Touches:
Floor it: A concrete floor is common in pole barns, but you can also go for wood, gravel, or even a combination. Consider what suits your needs and budget best.
Insulation and Climate Control: To make your pole barn more comfortable, consider adding insulation and ventilation systems, especially if you're using it as a workshop or living space.
Finishing Touches: Once the basics are in place, you can personalize your pole barn with windows, doors, lighting, and even a paint job. Make it your own!
Troubleshooting Tips and Tricks:
Safety First: Pole barn construction involves heavy lifting and power tools, so always prioritize safety. Wear protective gear, use ladders correctly, and be mindful of potential hazards.
Check Your Work: Throughout the process, double-check measurements and ensure all connections are secure. A little extra attention to detail can save you headaches later.
Don't Be Afraid to Ask for Help: If you're not confident about a specific step, don't hesitate to seek advice from a professional contractor or a seasoned DIYer.
Building a pole barn is a rewarding experience. It's a chance to unleash your creativity and create a space that perfectly suits your needs. Remember to take your time, plan carefully, and embrace the satisfaction of seeing your project come to life. And who knows, you might just discover a hidden talent for construction along the way!
How to Make a Pole Barn with High-Quality Materials
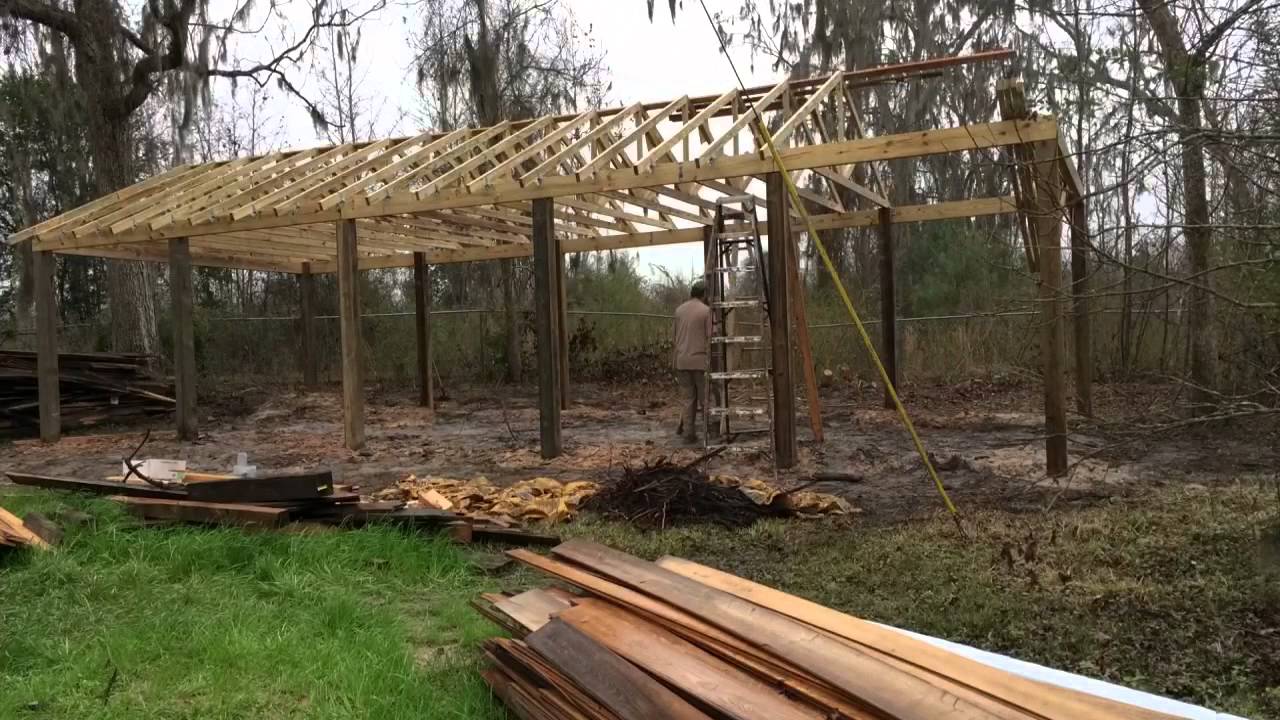
The pole barn, a versatile and robust structure, has long been a favored choice for diverse purposes, from agricultural storage to residential garages and workshops. However, achieving a truly durable and long-lasting pole barn necessitates a meticulous approach to material selection and construction. This article delves into the essential aspects of constructing a high-quality pole barn, emphasizing the importance of choosing premium materials for optimal performance and longevity.
1. Foundation: The Bedrock of Strength
The foundation forms the cornerstone of any pole barn, providing stability and longevity. While concrete is a conventional choice, a well-designed foundation can also be achieved with:
a. Concrete Piers: These provide excellent support for the pole barn. Ensure that the concrete piers are properly sized and reinforced with rebar to withstand the weight of the structure and any potential lateral forces.
b. Treated Timber Posts: For foundations in areas with frost heave or unstable soil, treated timber posts offer a durable and adaptable option. These posts should be deeply embedded and adequately spaced to guarantee stability.
c. Engineered Concrete Blocks: Durable and aesthetically pleasing, engineered concrete blocks provide a solid foundation while allowing for greater flexibility in design.
2. Poles: The Backbone of the Structure
The poles, or posts, form the primary support system for the pole barn. Opting for premium materials like pressure-treated lumber or engineered wood ensures a strong and long-lasting structure.
a. Pressure-Treated Lumber: This lumber undergoes a chemical treatment process that protects against decay, insects, and moisture, extending its lifespan significantly.
b. Engineered Wood: Products like laminated veneer lumber (LVL) offer exceptional strength and dimensional stability, making them an excellent choice for challenging conditions.
c. Steel Poles: While less common, steel poles offer outstanding strength and corrosion resistance, making them ideal for harsh environments or heavy loads.
3. Framing: Constructing a Solid Skeleton
The framing of the pole barn provides structural integrity and supports the roof and walls. Utilizing high-quality materials ensures strength and longevity:
a. Engineered Lumber: Products like laminated veneer lumber (LVL) and glulam beams provide exceptional strength and stability for the roof trusses and wall framing.
b. Steel Framing: While more expensive, steel framing offers unparalleled strength and resilience against fire and termites.
c. Treated Lumber: For framing components exposed to moisture, treated lumber ensures durability and resistance to decay.
4. Roofing: Protection Against the Elements
A robust roof system is paramount for protecting the pole barn from harsh weather conditions. Consider these options:
a. Metal Roofing: Durable, weather-resistant, and aesthetically pleasing, metal roofing offers excellent longevity.
b. Asphalt Shingles: Affordable and widely available, asphalt shingles provide effective protection, but their lifespan is shorter than metal roofing.
c. Standing Seam Metal Roofing: This type of roofing offers superior wind resistance and longevity, making it ideal for areas with high wind speeds.
5. Siding: Defining the Aesthetics and Durability
The siding of the pole barn determines its appearance and provides weather protection. Choose from:
a. Metal Siding: Durable, low-maintenance, and available in a variety of colors and finishes, metal siding offers excellent protection against harsh weather.
b. Vinyl Siding: An affordable option with a wide range of styles and colors, vinyl siding is moisture-resistant and easy to maintain.
c. Wood Siding: Provides a classic and natural look, but requires more maintenance than other options. Choose durable woods like cedar or redwood for extended longevity.
6. Windows and Doors: Balancing Aesthetics and Functionality
Windows and doors offer light, ventilation, and access to the pole barn. Choose high-quality options that provide the necessary features:
a. Aluminum Windows: Durable, weather-resistant, and low-maintenance, aluminum windows are a popular choice for pole barns.
b. Vinyl Windows: Affordable and efficient, vinyl windows offer excellent thermal performance and low maintenance requirements.
c. Steel Doors: Heavy-duty steel doors offer excellent security and durability, making them ideal for high-traffic areas.
7. Insulation and Ventilation: Creating a Comfortable Environment
Insulating and ventilating the pole barn ensures a comfortable interior environment and energy efficiency:
a. Fiberglass Insulation: Widely available and affordable, fiberglass insulation provides effective thermal resistance.
b. Spray Foam Insulation: Offers superior thermal performance and air sealing, reducing energy costs and improving comfort.
c. Ventilation Systems: Proper ventilation is crucial to prevent moisture buildup and ensure healthy air quality. Consider attic fans, gable vents, and soffit vents for optimal ventilation.
Conclusion: A Legacy of Durability
Constructing a pole barn with high-quality materials ensures a robust and long-lasting structure. By prioritizing premium materials for the foundation, poles, framing, roofing, siding, windows, doors, insulation, and ventilation, you can create a durable and functional space that will stand the test of time. Remember, investing in quality materials today will save you time, money, and headaches in the long run.
How to Build a Pole Barn with a Custom Foundation for Stability
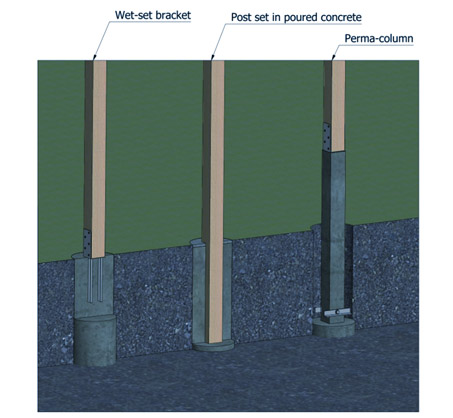
A pole barn, with its rustic charm and adaptable design, offers a versatile solution for a range of purposes, from workshops and garages to livestock shelters and storage facilities. However, achieving enduring stability and functionality requires careful consideration of the foundation. While traditional concrete piers or poured concrete slabs are common choices, exploring custom foundation options can elevate your pole barn to new heights of durability and longevity.
Understanding the Need for a Robust Foundation
Pole barns, unlike conventional structures with continuous wall supports, rely heavily on their foundation posts to bear the weight of the building and withstand environmental pressures. Neglecting the foundation can lead to a cascade of problems, including:
Structural Instability: Uneven settling or weak foundation posts can cause the barn to sag, crack, or even collapse.
Water Damage: Inadequate foundation drainage can lead to moisture intrusion, compromising the wood framing and creating an environment conducive to mold and rot.
Pest Infestations: Gaps or weaknesses in the foundation can provide entry points for rodents, insects, and other pests, jeopardizing the structural integrity and hygiene of the building.
Exploring Custom Foundation Solutions for Unwavering Stability
Custom foundation design allows you to tailor the structure to your specific site conditions and building needs. Here, we delve into the intricacies of different foundation types:
1. Engineered Pier Foundation:
Description: This approach involves installing deep, reinforced concrete piers that extend below the frost line, ensuring stability even in regions with freezing temperatures.
Advantages:
Superior load-bearing capacity.
Reduced susceptibility to frost heave.
Adaptable to challenging terrain.
Considerations:
Higher initial costs compared to simpler pier systems.
Requires specialized equipment for installation.
2. Insulated Concrete Forms (ICFs):
Description: ICFs are reusable plastic forms filled with concrete to create monolithic walls that provide exceptional insulation and strength.
Advantages:
Energy-efficient building envelope.
Enhanced resistance to moisture and pests.
Exceptional structural integrity.
Considerations:
Higher material and labor costs.
Requires specialized installation techniques.
3. Helical Pier Foundation:
Description: Helical piers are large-diameter screws that are driven into the ground, providing strong anchorage.
Advantages:
Cost-effective and efficient installation.
Minimal disruption to the surrounding landscape.
Suitable for challenging soil conditions, including clay and bedrock.
Considerations:
May not be ideal for extremely heavy structures.
Potential for soil disturbance during installation.
4. Combination Foundation Systems:
Description: Integrating different foundation types to maximize stability and cost-effectiveness. For instance, using helical piers for areas with loose soil and ICFs for sections requiring greater insulation.
Advantages:
Customized solution for unique site conditions.
Optimizes cost and performance based on specific needs.
Considerations:
Requires meticulous planning and coordination.
May necessitate specialized expertise for integration.
Steps to Design and Construct a Custom Foundation:
1. Site Assessment and Soil Testing: Conduct a thorough site analysis, including soil testing, to understand the bearing capacity, frost depth, and water table levels. This information is crucial for selecting the most appropriate foundation type.
2. Professional Engineering Consultation: Collaborate with a structural engineer to design a foundation that meets local building codes and addresses the specific load requirements of your pole barn.
3. Foundation Preparation: Clear the site, excavate to the specified depth, and ensure proper drainage is established around the foundation perimeter.
4. Installation and Reinforcement: Install the chosen foundation system, incorporating reinforcement bars or other strengthening elements as directed by the engineer.
5. Concrete Pouring and Curing: Pour the concrete for piers, ICFs, or slabs, allowing adequate time for curing and achieving full strength.
6. Final Inspection and Approval: Obtain final inspection and approval from the building department to ensure compliance with local regulations.
Considerations for Long-Term Performance:
Drainage and Waterproofing: Implement a comprehensive drainage system around the foundation to divert rainwater and prevent moisture accumulation. Utilize waterproofing materials to seal any potential entry points for water.
Pest Control: Consider using pest-resistant materials and techniques during foundation construction. Install screens or barriers to prevent entry and implement regular pest control measures.
Maintenance and Monitoring: Regular inspections and maintenance are crucial for identifying potential problems early. Address any cracks, settlements, or water damage promptly to prevent escalation.
Conclusion:
Constructing a pole barn with a custom foundation is an investment in long-term stability and functionality. By meticulously planning, engaging qualified professionals, and implementing best practices, you can ensure your barn stands the test of time, providing a robust and reliable structure for years to come. Remember, a well-designed and executed foundation is the cornerstone of a strong and enduring pole barn.